In the metal stamping industry, tool dies are critical for producing accurate, high-quality parts. However, the repetitive pressure and wear from stamping operations can gradually degrade these tools. Over time, worn dies may produce parts with increased error margins—or worse, lead to misshapen or defective products. That’s why routine die repair and maintenance is essential to maintaining precision, reducing downtime, and extending the lifespan of your tooling.
Ultimately, the quality of your stamped part depends on the quality of your die, and proactive maintenance is the key to protecting that quality.
What Is Die Maintenance?
The first step in ensuring consistent quality and long-term tool performance is incorporating a preventive die maintenance program into your stamping workflow. Without regular care, die can suffer from buildup, misalignment, or damage that leads to costly production issues.
Here’s a breakdown of the four essential steps in proper die maintenance:
1. Cleaning
Routine cleaning removes metal shavings, lubricants, and debris that collect on die surfaces and in cavities. Skipping this step can accelerate wear and result in cosmetic or dimensional flaws in your parts. Regular cleaning also makes it easier to detect early signs of damage.
2. Inspection
Detailed, scheduled inspections catch early wear, cracking, or misalignment before it leads to costly downtime. Technicians should evaluate all critical surfaces—cut edges, punches, dies, and guide pins—using magnification or precise measuring tools to ensure nothing is missed.
3. Repair
Addressing small problems before they grow ensures production stays on track. Common repairs include sharpening cutting edges, replacing worn components, adjusting alignment, and welding minor cracks. Timely die repair restores proper function and protects stamping accuracy.
4. Protection
After maintenance, dies should be coated with rust inhibitors and stored in a clean, dry, controlled environment. Protective packaging or storage covers can help prevent damage during downtime. Establishing a consistent storage routine helps preserve die conditions between runs.
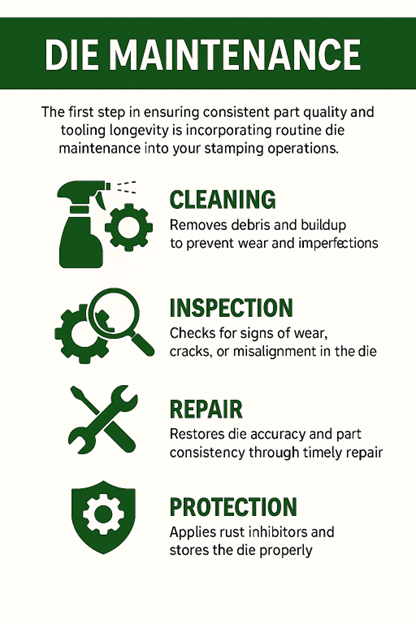
Key Benefits of Regular Die Maintenance
Implementing a consistent die maintenance and repair schedle offers numerous advantages for stamping operations:
- Extended Die Life – Reduces wear and damage to maximize tooling lifespan.
- Consistent Part Quality – Maintains part accuracy and finish, reducing rework and scrap.
- Reduced Downtime – Prevents breakdowns and production delays.
- Cost Savings – Avoids expensive repairs or replacements with proactive upkeep.
- Improved Efficiency – Keeps stamping lines running smoothly and reliably.
- Enhanced Operator Safety – Prevents hazards caused by tool failure.
- Optimized Tooling Performance – Supports alignment, clean cuts, and precision stamping.
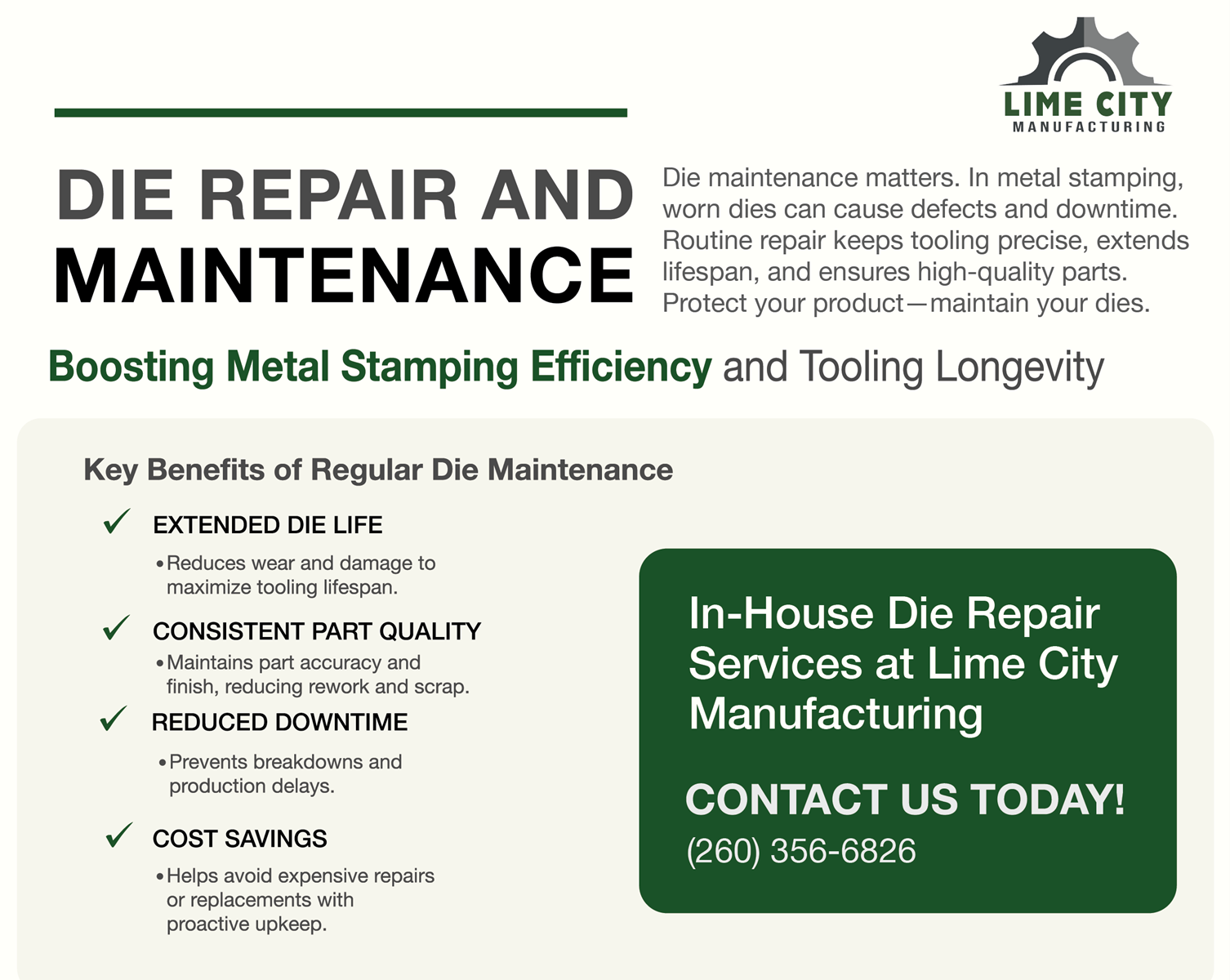
In-House Die Repair Services at Lime City Manufacturing
At Lime City Manufacturing, we support your production with expert in-house die repair and maintenance services. Our on-site tool room is staffed with a die technician who has over 20 years of experience, ensuring your tooling gets expert care when you need it.
We also keep critical spare parts on hand to reduce downtime and get your die back in service quickly. This keeps your stamping operations moving—and your parts delivered on time and in excellent condition.
Contact us today to learn more about our metal stamping services and how die maintenance solutions from Lime City can improve your production line.